Sustainable
Development
»
Environment
Key Indicators
7.05
Reducing the consumption
of fuel and energy resources
KEGOC issued its first green bonds. KEGOC successfully placed green bonds on KASE in December 2022 with a total volume of KZT 16.1 billion and a margin of 3%.
3.28
Reduced consumption of
gasoline and diesel fuel
KEGOC has developed a 2060 Carbon Footprint Reduction Programme.
Management system
Key documents |
|
|
|
|
|
|
|
KEGOC Board of Directors agenda
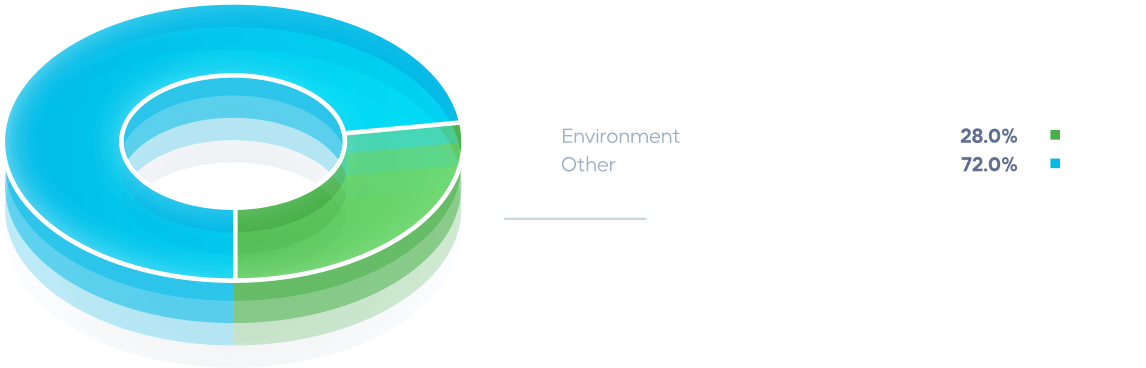
Occupational Health, Safety and
Environmental Protection Committee agenda
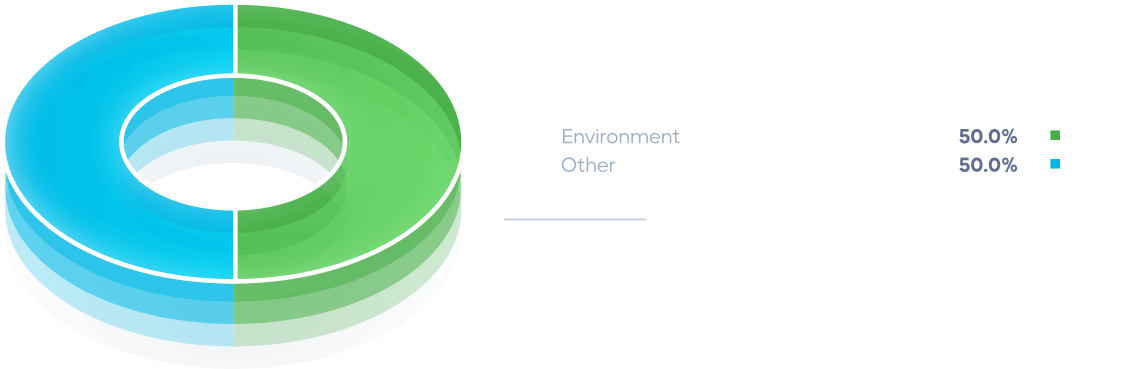
KEGOC Management Board agenda
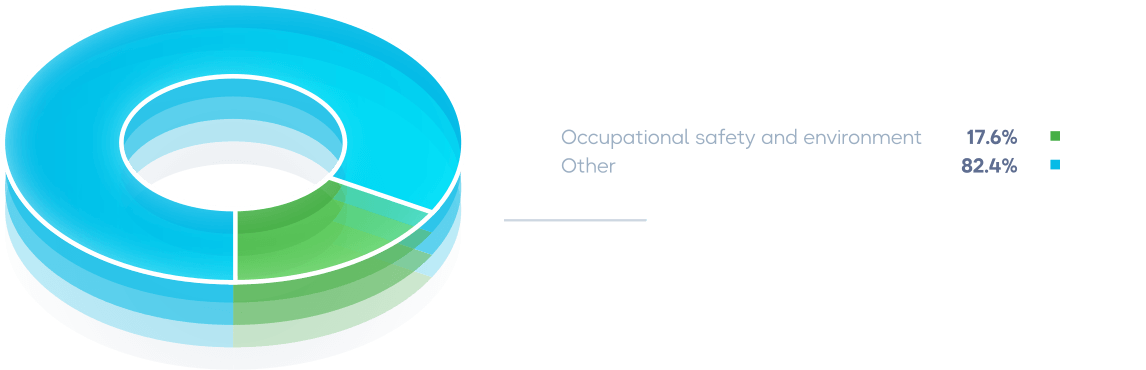
Environmental
Policy
KEGOC considers environmental activities as an integral part of its day-to-day operations. Environmental responsibility is a key principle of KEGOC Environmental Policy.
The goals of the KEGOC Environmental Policy are to minimise negative environmental impact, increase environmental safety, take responsibility for the environmental security of Kazakhstan National Grid development, promote energy savings, and rational use of environmental and energy resources in the Company’s operations. KEGOC’s management takes the responsibility for implementation of obligations taken in accordance with Environmental Policy on continuous improvement and pollution prevention, as well as obligation to meet applicable legislative and other requirements related to KEGOC in terms of its environmental aspects. All employees of the Company as well as employees of contractors working for the Company shall review KEGOC’s Environmental Policy.
The Company implemented the environmental management system, which is certified for compliance with the requirements of international standard ISO 14001. The system operates as part of KEGOC’s integrated management system. The primary goal of its implementation and operation is to adopt innovative management approaches in order to have a greater impact on the environmental aspects of the Company’s operational and economic activities. The environmental aspects management is a component of the corporate risk management system in KEGOC.
For efficient management, the Company developed registers of its environmental aspects for 2022. To identify the aspects, the Company analyses all components of the environmental impact (energy saving, water, soil, emissions, waste). Activities to manage environmental aspects are specified in the Company’s Environmental Program for 2022. In 2022, ‘waste potentially containing polychlorinated biphenyls (PCBs),’ ‘transformer oil,’ and ‘waste transformer oil’ were recognised as key environmental aspects. “Waste potentially containing polychlorinated biphenyls (PCBs)” aspect is significant because the Environmental Code of the Republic of Kazakhstan recognize polychlorinated biphenyl as a hazardous substance. The ‘spent transformer oil’ and ‘transformer oil’ aspects are critical due to the existence of oil-filled equipment.
Ambient Air Impact
According to a recent amendment of the Kazakhstani Environmental Code, the authorised body for environmental protection has classified the majority of MES branches as items falling under category IV, for which there are no specified emission criteria.
However, an internal Environmental Control Programme was created to monitor the branches, and in 2022, stationary source emissions reports were generated in the MES branches on a quarterly basis. The number of operating hours of each piece of equipment and the amount of materials consumed were used as the basis for the calculation of pollutant emissions.
In category II branches the environmental monitoring has been done by expert entities using calculations or laboratory measurements.
Gross emissions of pollutants from stationary sources totalled 9.34 tonnes in 2022 vs the regulatory limit of 11.63 tonnes. Thus, gross emissions from stationary sources (with regard to standard rate) dropped by 20%.
According to the Code of the Republic of Kazakhstan “On taxes and other mandatory payments to the budget” the emissions from mobile sources shall not be measured, reports shall specify the amount of the used fuel. The vehicles were tested for toxicity and opacity of exhaust gas.
The Company does not emit any ozone-depleting substances influencing the climate change.
Ensuring the decarbonization of the economy through the development and integration of RES into Kazakhstan’s energy system are the main business’s strategic goals and objectives, as well as the most significant beneficial environmental impact of KEGOC as a network company and System Operator.
To mitigate transitional climate risk in 2022, the Company adopted its 2031 Low-Carbon Development Programme and a 2060 carbon neutrality vision based on Kazakhstan’s 2060 Strategy for Achieving Carbon Neutrality, Samruk-Kazyna JSC’s Low-Carbon Development Concept, and KEGOC’s 2022-2031 Development Strategy.
KEGOC contributes to the reduction of greenhouse gas emissions in accordance with the Development Strategy of Samruk-Kazyna JSC for 2022-2031, which aims to reduce the carbon footprint in the Fund’s group of firms to 10% by 2031. The incorporation of the low-carbon agenda will allow the Company to contribute not only as a network company and System Operator connecting renewable energy sources, but also to increase KEGOC’s investment attractiveness, competitiveness in the context of the energy transition, and declare the Company’s climate ambitions.
The Programme’s goal is to systematise the primary approaches and actions for reducing the carbon footprint, including:
- Analysis and evaluation of capability and potential to lower the current business’s carbon footprint;
- Identification of key decarbonization areas and actions to reduce the carbon footprint
- Forecasting of trends in CO2 emissions up to 2060;
- Raising of the awareness of the Company’s personnel, including about ongoing global trends in reducing the carbon footprint.
The current situation has been examined as part of the Programme development, and the main sources and indicators of direct and indirect CO2 emissions (Scopes 1 and 2) have been identified, including actions to reduce the Company’s carbon footprint of its operations and key indicators to monitor the carbon footprint reduction.
The following are the primary sources of direct greenhouse gas emissions (Scope 1) in KEGOC:
- mobile sources, vehicles utilised in the execution of the main categories of business operations, including maintenance and repair;
- stationary sources, stationary and portable power plants, and generators of electrical energy used to assure the reliability of power supply in communication facility emergency situations, as well as during maintenance and repair operations.
- SF6 circuit breakers, a necessary piece of substation equipment for KEGOC’s Intersystem Electric Networks branches.
Indirect emission sources (Scope 2) include:
- emissions generated during the generation of electricity purchased by the Company for technological purposes, including compensation of the technical losses of electricity during its transmission through Kazakhstan NPG, as well as auxiliary consumption of heating, lighting of buildings, premises, territories and etc.
- emissions generated during the generation of heat purchased by the Company for heating of industrial and non-industrial premises.
As System Operator and grid operator, the Company is not permitted to develop or implement its own renewable generating or RES construction projects, as this would create a potential conflict of interest in the fulfilment of the System Operator functions of the UPS of Kazakhstan.
The Company sees the key measure of its own Carbon Footprint Reduction Programme as the purchase of green electricity through:
- country scheme to support the implementation of RES projects in accordance with the current legislation (current at about 4%) and / or
- bilateral contracts for existing and prospective renewable energy facilities.
Another important focus of the Programme will be the implementation of necessary resource and energy efficiency measures with corresponding potential energy saving and energy efficiency measures. E.g., the main mechanisms for implementing the Programme will be energy audits, both present and future, the development of energy efficiency actions, and the implementation of energy efficiency and resource efficiency programmes.
It is also worth noting that the best results of the Company in the area of resource saving and energy efficiency include the introduction of an energy efficiency policy and tools to motivate Company employees to make rationalisation proposals, introduction of new technologies through R&D, implementation of pilot projects and tests.
The Programme sets out the low-carbon development targets by 2031:
- for Scope 1 (direct emissions): gradual replacement of passenger cars with internal combustion engines with similar modes of transport using low-carbon fuels (electric vehicles, LPG) to achieve a 2% reduction in emissions by 2030;
- for Scope 2 (indirect emissions): gradual increase the share of ‘green’ RES electricity to compensate for losses in KEGOC’s networks and reach 20% by 2031.
According to the Environmental Code of Kazakhstan, ‘A quotable installation is an installation whose quota greenhouse gas emissions exceed twenty thousand tonnes of carbon dioxide per year in the regulated sectors of the economy’. KEGOC is not subject to quotas. However, in accordance with the terms of the UN Framework Convention on Climate Change, the Kyoto Protocol, the Paris Agreement following the results of 2022, KEGOC developed and verified the Greenhouse Gas Emissions Inventory Report. The data is consolidated at the corporate level using an operational approach. It includes greenhouse gases: CO2, CH4, N2O, SF6. Greenhouse gas emissions from air conditioning systems are excluded from Scope1 emissions due to insufficient data and their insignificance. Scope 3 greenhouse gas emissions are not included in the report due to insufficient data.
The base year 2022 is chosen as the GHG Protocol Greenhouse Gas Inventory Report has been prepared by KEGOC for the first time. The base year will be recalculated if a new category is added or if a switch to a more accurate methodology is made.
Emission factors are calculated according to the IPCC Guidelines for National Greenhouse Gas Inventories for the Electricity Sector (Intergovernmental Panel on Climate Change (IPCC)); the climate change factors are taken from the Report of the Nineteenth Session of the UN Working Group on Climate Change.
Emissions | Total | CO2 | CH4 | N2O | SF6 |
t CO2 eqv | т | т CO2 eqv | т CO2 eqv | т CO2 eqv | |
Scope 1 | 8,887 | 8,721 | 40 | 126 | 0 |
Scope 2 | 2,632,728 | 2,632,72 | - | - | 0 |
The majority of Scope 2 indirect emissions are created during the generation of power acquired by the Company to compensate for the technological consumption of electricity during its transmission through Kazakhstan’s NPG (transmission losses). The amount of technology consumption is proportional to the length of transit transmission lines and is determined by the operational states of neighbouring nations’ energy systems (transit, export and import of power), climatic circumstances, and cannot be avoided by the Company.
The 2022 Greenhouse Gas Inventory Report (Scope 1, Scope 2) has been validated by the validation and verification body in accordance with the requirements of ST RK ISO 14064-3-2019 for compliance with the Greenhouse Gas Protocol (GHG Protocol), WRI/WBCSD GRI 305 Emissions 2016, CDP Climate Change 2021 Reporting Guidance on a reasonable assurance basis with a 2% materiality level.
The Company uses SF6 equipment such as SF6 circuit breakers. Modern 110-500 kV SF6 circuit breakers built by ABB, Siemens, and GE have been installed in substations as part of the company’s technical upgrading. They are of high quality, reliable, and ecologically friendly.
The SF6 circuit breakers are operated in strict accordance with the instructions and regulations; the use of SF6 gas is monitored and managed; there was an average yearly leakage rate of 0.03% from 2016 to 2022; there was no leakage in 2022.
There are currently no 220-500 kV vacuum circuit breakers available, and SF6 circuit breakers are the only option in this voltage class. Since the use of 110 kV vacuum circuit breakers is not common throughout the world, the Company does not currently use these breakers.
However, the use of ecologically friendly vacuum circuit breakers with a voltage range of 6-10-35 kV in substations helps to limit the usage of SF6 in rehabilitation projects.
The specific greenhouse gas emission factor (total for Scope 1 and Scope 2) is 0.045 tonnes of CO2 per MWh of transmitted electricity.
In 2022, in order to contribute to improving the environment and supporting global trends in reducing the carbon footprint, the Company’s employees planted about 570 seedlings of trees and shrubs in Astana, in the Almaty, Western and Northern regions of Kazakhstan.
Waste Management
The Company generates production wastes during substation equipment operation, maintenance, and rehabilitation. The Environmental Code of Kazakhstan and KEGOC’s Waste Management Organisation Standard, which classifies all waste as hazardous and non-hazardous, are followed when managing waste at the Company.
Waste Volume in KEGOC Divisions
Description, tonnes | 2022 |
Hazardous waste | 11.312 |
Non-hazardous waste | 2,624.673 |
Total | 2,635.985 |
To help reduce waste, the Company’s employees engaged in a waste paper collection initiative in 2022, and together with the ‘Assistance to People in Need’ Charity Fund gathered 960 kg of material for further recycling and reuse. The proceeds were used for the needs of the Orphanage in Astana.
Water Body Impact
Water is not used in the Company’s technological process. The Company’s water usage is negligible, and KEGOC operations have no major impact on used water sources. There are no discharges into water facilities and relief. 7 branches of KEGOC have artesian water supply and wells are operated in accordance with the permits obtained.
Biodiversity Impact
As a power grid company and system operator, KEGOC has no significant impact on fauna and flora.
The Company adopts a holistic approach to environmental protection and biodiversity conservation when completing projects, including investment initiatives.
To manage environmental risks during the design stage of power grid facilities, overhead line routes and substation sites are prohibited from passing through settlement lands and territories, including those designated for future development of villages, settlements and cities, as well as those intended for agricultural development, natural reserves, forest farms, water protection zones, irrigated farmlands, specially protected territories and cultural heritage sites. The majority of the overhead lines travel through steppe and semi-desert areas.
KEGOC functions in accordance with the principles of Kazakhstan’s environmental legislation, particularly the concepts of environmental information accessibility and public engagement. When any construction or reconstruction projects are being considered, public hearings or debates on the project EIA are required.
The EIA considers all processes that could have a substantial environmental impact on the planned activity, such as air, water bodies, and groundwater, terrain, biodiversity conservation, and wildlife. Project risks are identified and assessed on a continual basis and at all phases of project implementation. PESTEL analysis is used to assess project hazards, including social and environmental concerns. The results of the environmental impact assessment, including biodiversity, are considered, and the alternative that causes the least environmental harm is chosen.
The beneficial influence of KEGOC on biodiversity is that it promotes the conservation of traditional habitats in power line right-of-ways and sanitary zones near substations.
According to global studies, power lines with voltages ranging from 0.4 to 10 kV are hazardous to birds due to the short distances between the earthed cross-arm or other earthed areas of the transmission tower and live conductors. Birds can cause a fatal short-circuit when they brush an earthed cross-arm and a live conductor while lifting off or flying by.
99.4% of KEGOC’s overhead lines are high-voltage lines of 110 kV or above, with a minimum distance of 1.5 metres between earthed and current-carrying parts of the overhead lines. As a result, such line design effectively eliminates the risk of electric shock to birds and bats because the wingspan of birds cannot close the gap the conductors and earthed parts of a line. However, in areas where birds may land on the traverse of the lines, KEGOC has installed more than 7,000 unique bird-protection devices.
Energy Efficiency
KEGOC’s main goals in energy saving and energy efficiency improvement are to reduce the volume of consumed fuel and energy resources, including by reducing auxiliary energy consumption at KEGOC facilities, reducing technological losses of electricity in the NPG, improving energy consumption control mechanisms and equipment of Company facilities with electricity and other fuel and energy resource metres, and organising information collection on energy consumption.
Fuel and energy consumption in 2022, GJ 1
Electricity | 10,169,639.51 |
Heat power | 84,842.87 |
Fuel | 120,145.7 |
including: | |
|
40,918.42 |
|
75,481.13 |
|
3,237.41 |
|
508.78 |
Total | 10,374,628.12 |
1 When converted to Joul, the international system of units (SI) was used.
Fuel and energy consumption in 2022 declined by 788,170.43 GJ compared to 2021 due to a decrease in supply to the grid and, as a result, a decrease in electricity losses.
In 2022, specific energy consumption amounted to 0.18 GJ per 1,000 kWh of transmitted electricity.
The most effective, in terms of reducing the energy consumption, are the measures on reduction of technological consumption of electricity in transmission lines.
Kazakhstan’s electric power system is best known for the concentration of large energy sources in the grid’s Zone North and the long (approximately 1,000 km) transmission lines (mainly connecting Kazakhstan’s northern and southern regions, as well as Pavlodar and Aktobe oblasts) - this is due to the country’s large territory and has a significant impact on the level of technological electricity consumption (technical losses). The technical losses in KEGOC’s network also depend on the operation states of energy systems of neighbouring countries (transit, export and import of electricity) and climatic conditions.
Structure of electricity
losses of KEGOC for 2022
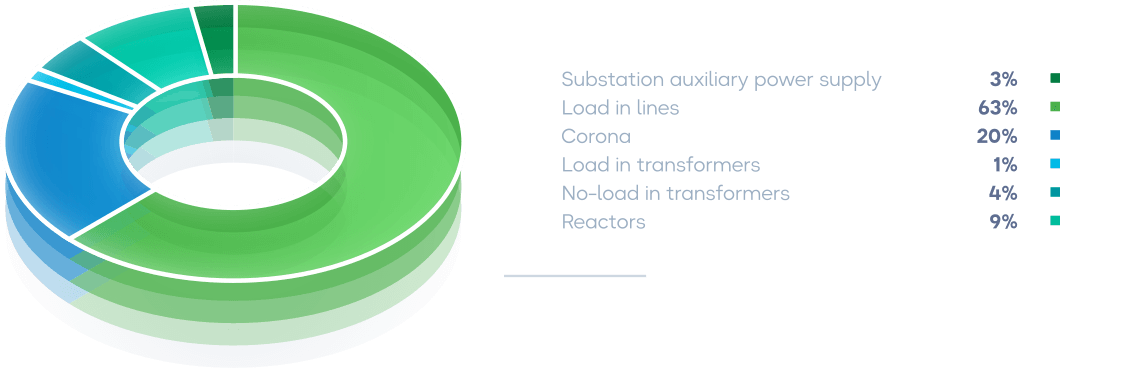
The technical losses in KEGOC networks in 2022 amounted to 2.796 billion kWh or 4.9% of electricity supply to the grid.
It should be understood that technical loss of electric power means the loss of electric power resulting from the physical processes in conductors and electrical equipment which occur during the electricity transmission across transmission lines. Thus, the main goal of planning and taking the measures on reduction of electric power losses is to bring the actual amounts of technological loss to its optimal level.
The risk of excessive losses in power transmission could increase as a result of climate change. Therefore, when developing measures to mitigate this risk, as well as to reduce electricity losses, the Company analyses climatic factors and analyses actual electricity losses in KEGOC’s networks.
Due to measures on electricity loss reduction implemented, in 2022 the reduction of electricity consumption amounted to 3.932 million kWh.
Activity | Outcomes | |
mln kWh | GJ | |
Line tripping under low-load conditions | 0.260 | 936 |
Shutdown of power transformers under low load conditions | 3.672 | 13,219 |
Total for KEGOC | 3.932 | 14,155 |
HR Policy
Key Indicators
86
Social
stability (SRS)
On the occasion of KEGOC’s 25th anniversary, 1,047 employees received awards and commemorative medals for their special services, and a one-time bonus was paid to all employees.
8.13
Personnel
turnover
Employees’ salaries were increased.
Management system
Key documents |
|
|
|
|
|
|
|
|
|
|
|
KEGOC Board of Directors agenda
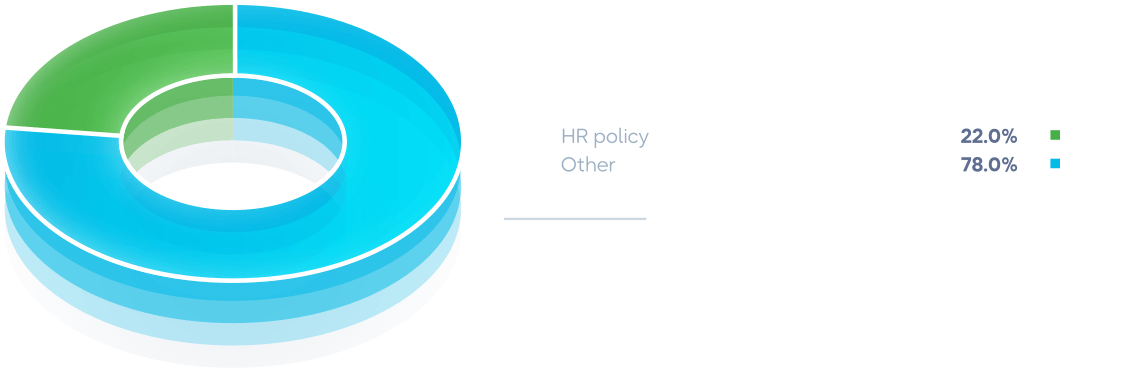
KEGOC Management Board agenda
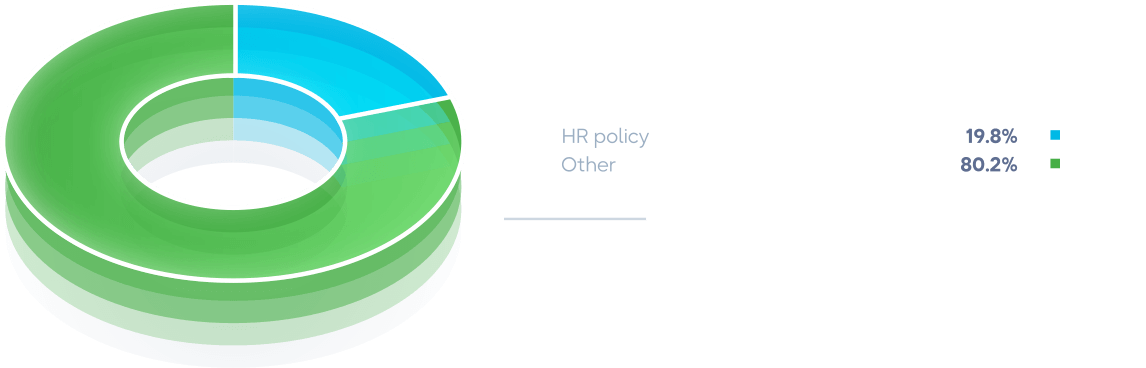
Nomination and Remuneration Committee agenda
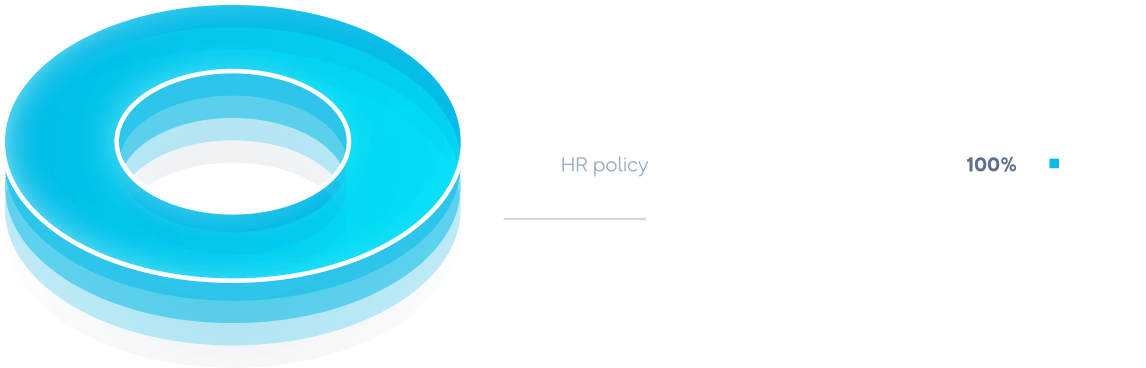
The human resources of KEGOC are the most important strategic factor for the Company’s development success. KEGOC manages its human resources based on the principles of the Corporate Governance Code, Code of Conduct (Business Ethics Code), the integrated management system, HR Policy and internal documents relating to KEGOC’s HR motivation.
Descriptionя | 2018 | 2019 | 2020 | 2021 | 2022 |
SRS index | 85 | 90 | 91 | 85 | 86 |
Personnel Structure
The Company’s headcount (including subsidiaries) as at 31 December 2022 was 4,376 employees.
Number of employees
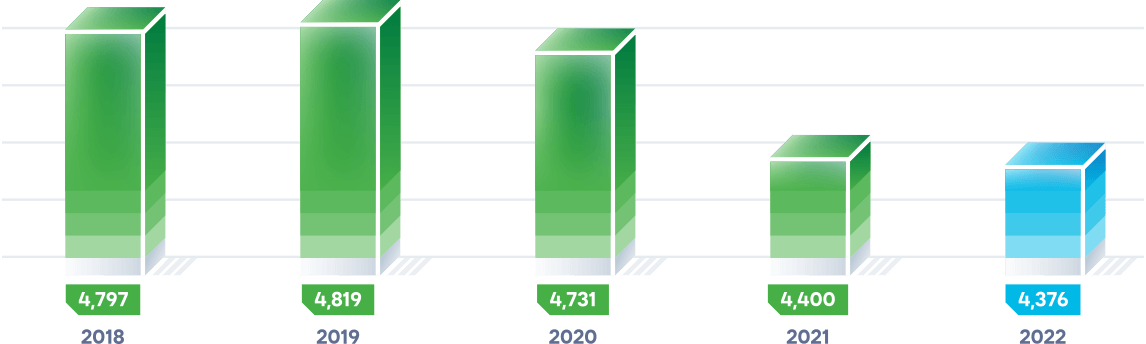
Personnel structure by region
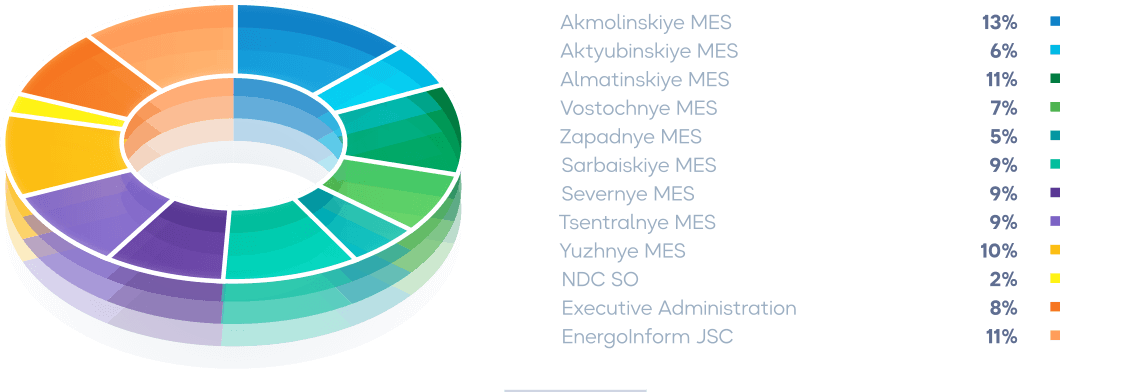
Personnel structure by age
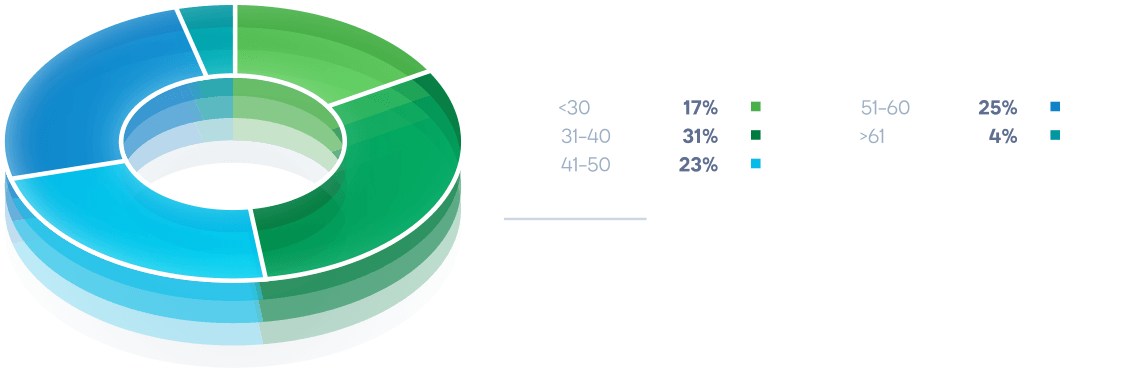
Personnel structure by length of service

Personnel structure by ethnic origin
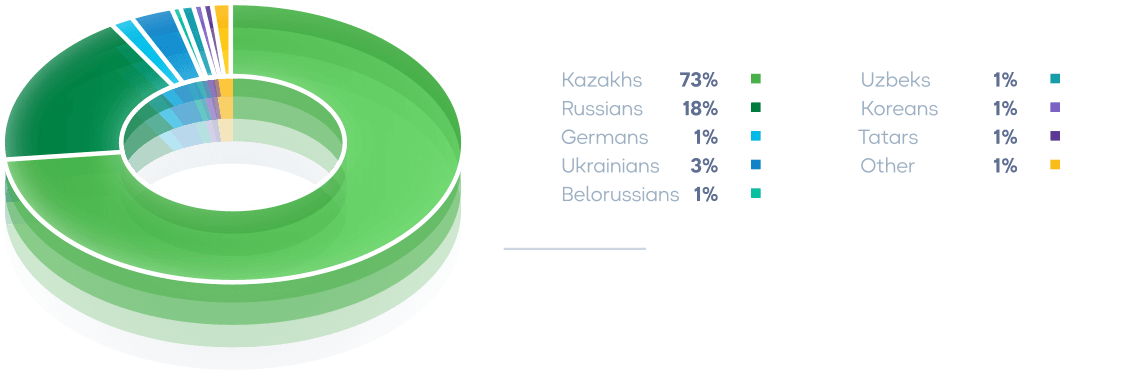
Personnel structure by employment
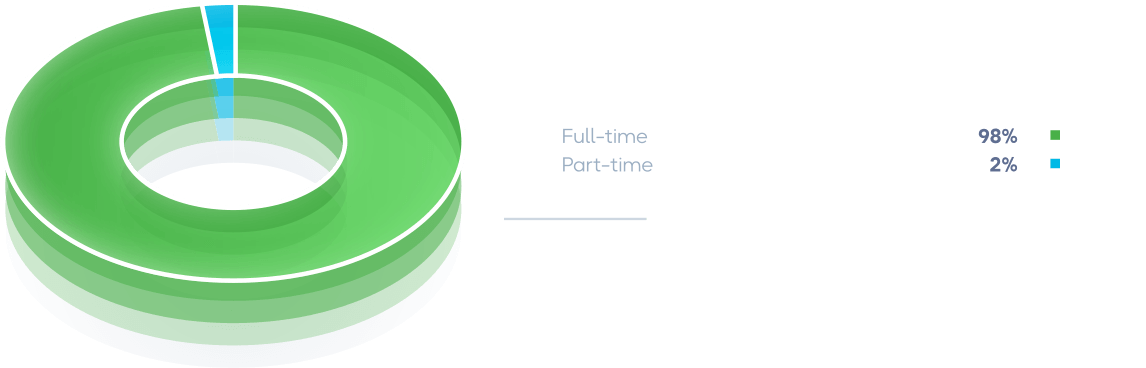
Personnel structure by gender
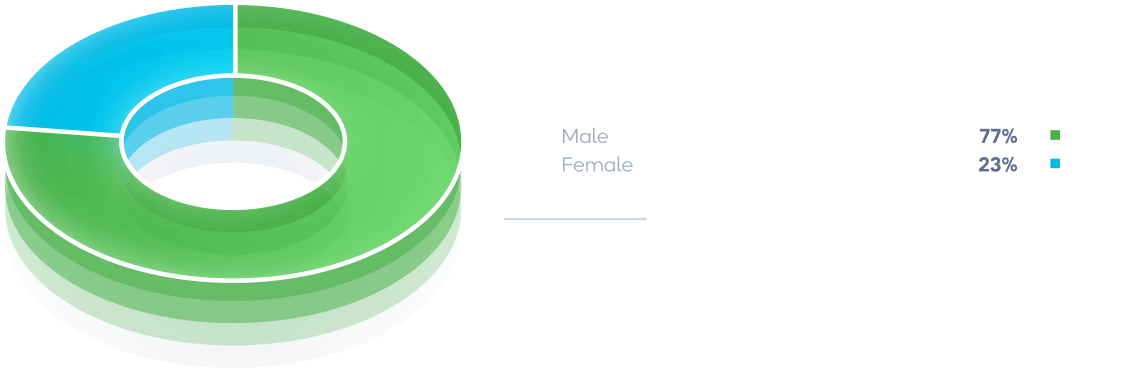
Personnel structure by category
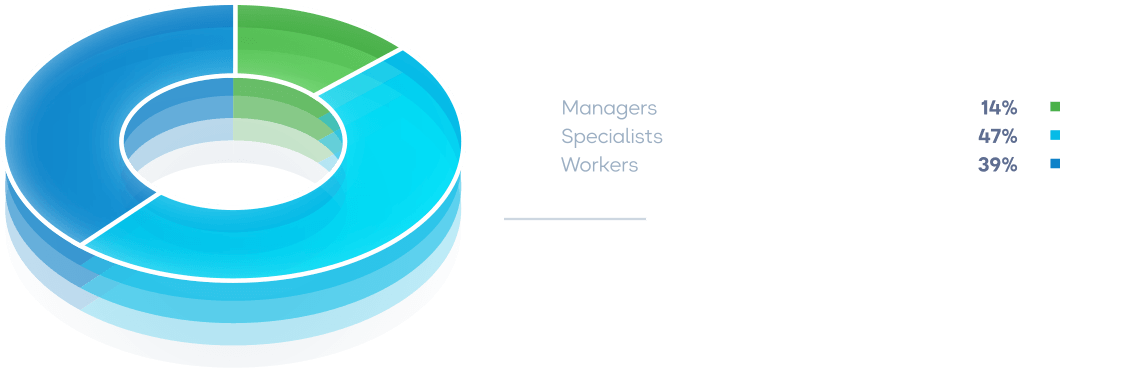
Personnel structure by education
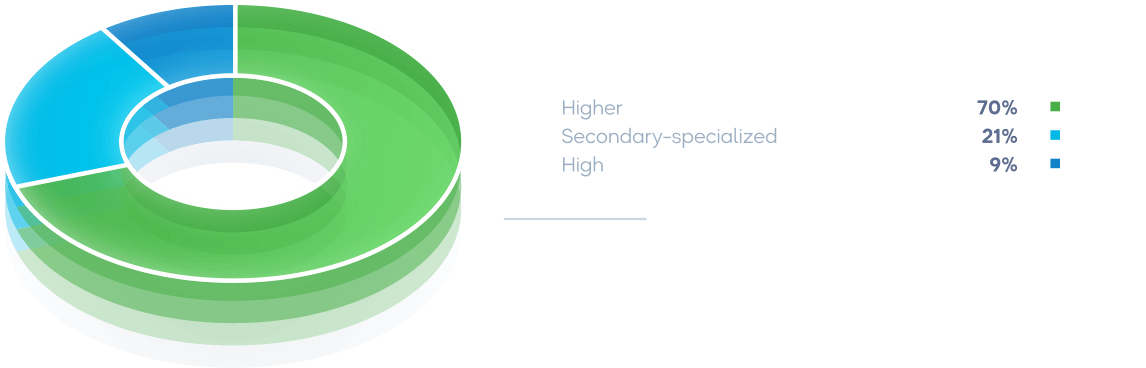
Indicator | Total | Proportion, % | AM | Operational | Managers | Management proportion, % | |
Number of people on the payroll | 4,376 | 100 | 535 | 3,841 | 619 | 100.0 | |
Gender | men | 3,367 | 76.9 | 166 | 3,201 | 552 | 89.2 |
women | 1,009 | 23.1 | 369 | 640 | 67 | 10.8 | |
Ethnic groups |
kazakh | 3,179 | 72.6 | 463 | 2,716 | 451 | 72.9 |
russian | 802 | 18.3 | 46 | 756 | 110 | 17.8 | |
ukrainian | 123 | 2.8 | 4 | 119 | 19 | 3.1 | |
tatar | 62 | 1.4 | 5 | 57 | 12 | 1.9 | |
germans | 57 | 1.3 | 4 | 53 | 7 | 1.1 | |
other | 153 | 3.5 | 13 | 140 | 20 | 3.2 | |
Age groups | under 30 | 730 | 16.7 | 53 | 677 | 49 | 7.9 |
30 to 50 | 2,319 | 53.0 | 376 | 1,943 | 355 | 57.4 | |
over 50 | 1,327 | 30.3 | 106 | 1,221 | 215 | 34.7 | |
The total proportion of senior executives (members of KEGOC’s Board of Directors and Management Board) hired from the local community (citizens of Kazakhstan) is 90.9% as at 31 December 2022.
Personnel turnover
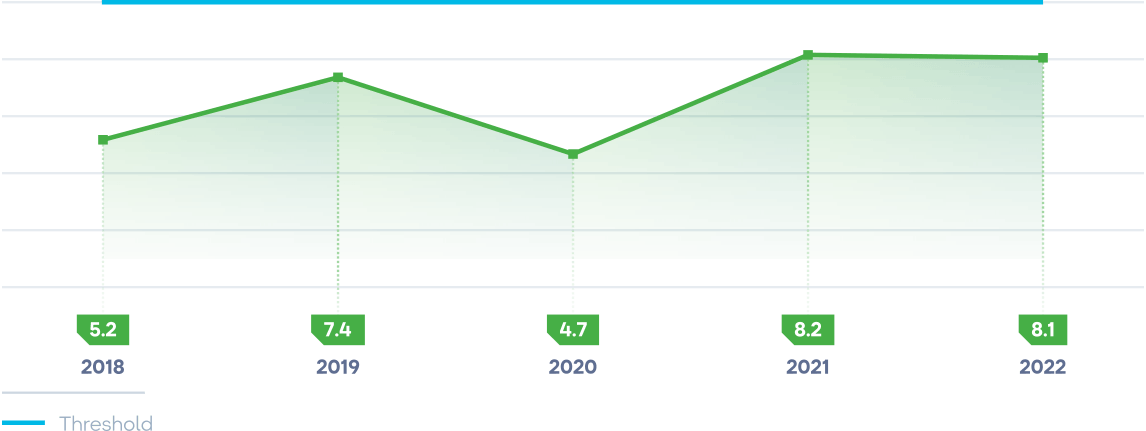
Personnel in 2022
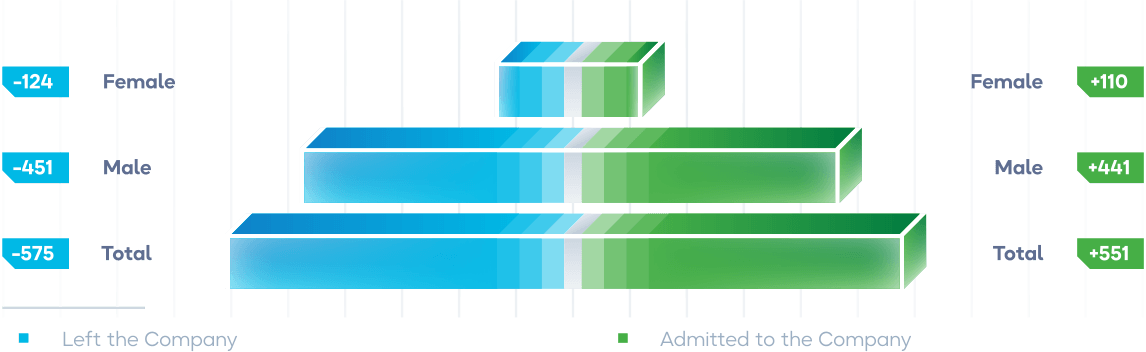
Duration of Work of KEGOC Employees who Left the Company in 2022
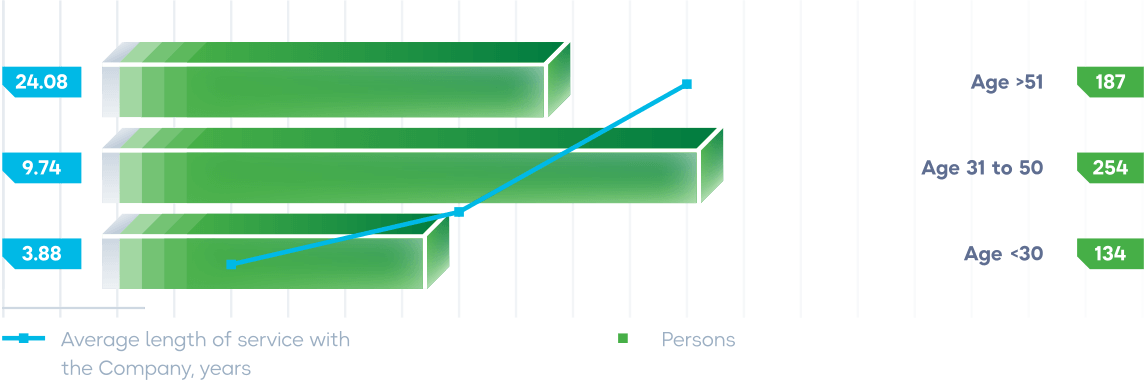
The actual KEGOC staff turnover rate for 2022 was 8.13%, falling under the predetermined limit of 10%. The turnover rate for men was 7.35% and 3.23% for women. Average work duration of male employees quitted KEGOC in 2022, was 13.5 years (451 employees), and female employees 14.2 years (124 employees).
The following preventive actions are taken by the company to manage the risk of employee turnover:
- provision of social support, promotion and recognition of merits, procedures for talent management, training and development;
- monitoring of average market wages, improvement of the wage system;
- conducting social ranking surveys.
Recruitment Policy
KEGOC provides equal opportunities to all candidates regardless of their nationality, race, gender, age, marital and social status or other distinguishing characteristics.
Personnel Development
KEGOC attaches great importance to training.
2,385 employees were trained in the reporting year, which is 54.5% of the total headcount. Actual training expenditures of KEGOC in 2022 amounted to KZT 182.5 million or 54.5% of the plan, which is 43.4% more than in 2021.
The total number of training hours was 110,534.0 hours, of which 96,938.5 hours were for men and 13,595.5 hours for women; 14,890 hours for administrative and managerial employees, and 95,644 hours for operational employees.
The average annual number of training hours per employee was 27.6 hours, including 27.1 hours for administrative and managerial employees and 27.6 hours for operational employees.
The average number of training hours per employee was 27.7 hours for men and 26.9 hours for women.
To improve the level of professional knowledge, skills, and abilities of young operational personnel, to assist them in their professional development, to retain the competences of experienced operational personnel, to adapt to the corporate culture, to learn the traditions and rules of conduct, KEGOC has introduced and operates a mentoring system. The Company annually holds ‘The Best Mentor of the Year’ competition.
KEGOC’s talent pool is being systematically built up: the functional and management succession pools of 219 persons have been approved.
Collective Bargaining Agreement and Trade Union Activities
KEGOC supports freedom of association and recognises the right of employees to bargain collectively.
The collective bargaining agreement, developed after considering the suggestions of all Company employees, was reached between KEGOC and its labour collective for the years 2021–2025. It specifies procedures for accession, labour schedule regulation, including time off for social leaves, labour remuneration, ensuring labour safety and health protection of employees, social guarantees and compensations, measures for employee support and development of human resource potential, medical insurance, and cultural leisure activities. It also includes new amendments and additions pertaining to the provision of special clothing, special footwear, and other personal protective equipment to employees at the expense of the Company, as well as issues pertaining to social support of veterans of the Great Patriotic War and persons equated to them, veterans of power engineers, who are registered with the Company.
The collective bargaining agreement shall apply to all KEGOC employees (100%) irrespective of the type of employment.
The trade union congress of KEGOC employees on March 27, 2003, led to the establishment of EnergoTekhProfSoyuz, the organisation representing workers in the energy sector. The purpose of this trade union is to oversee the preservation and application of guarantees, remuneration, and benefits, as well as compliance with labour laws.
Today, the structure of EnergoTekhProfSoyuz has 10 primary trade union organisations. The total number of KEGOC employees’ trade union organisation members is more than 3,600, i.e., more than 90% of the Company’s employees.
Six standing committees have been set up within the trade union committee:
- cultural affairs committee;
- sports affairs committee;
- recreational affairs committee;
- youth affairs committee;
- veterans’ affairs committee;
- health and safety committee.
In addition, there are five joint commissions set up on a parity basis by the trade union and the employer:
- collective bargaining commission;
- conciliation commission;
- operational affairs council;
- awards committee;
- committee for summarising the results of the Labour Dynasties and Occupational Safety and Health competitions.
As a member of the Republican Association of Trade Unions of the Kazakhstan Confederation of Labour, our trade union organisation is a permanent member of the working committee and actively participates in the work of the Commission of the Ministry of Labour and Social Relations of Kazakhstan on the Labour Code and the Law on Trade Unions, and participated in the drafting of the General Agreement, the draft Social Code of Kazakhstan, and the draft Sectoral Agreement.
Trade unions pay special attention to health and safety issues. Public inspectors visit the Company’s facilities, the results of which are carefully reviewed. For instance, changes to the collective bargaining agreement were made in response to employee requests to upgrade video recording equipment for work on power lines and substations and to provide some staff with safety gear. Competitions for workplace safety were held in 2022, including ‘Best Mentor of the Year’ and ‘Best Branch in Observance of Occupational Safety.’
Trade union members benefit from discounts on recreational vouchers to health resorts in Kazakhstan, with approximately 120-140 employees treated there each year and over 400 trade union members treated in recreational facilities.
The trade union organisation works hard to create a healthy social environment in the workforce. Thus, in 2022 KEGOC celebrated its 25th anniversary. For the first time, a family holiday was organised for the Company’s employees in Borovoye resort area.
Great attention is paid to veterans of the power industry and participants of the Great Patriotic War: financial and material support is provided; preferential recreational vouchers are provided; they are invited to all events held by the Company. As part of KEGOC’s 25th anniversary celebrations, more than 140 veterans who are retired from the Company were awarded a jubilee medal.
The Company maintains the record of:
- 58 participants in the Second World War and persons of equivalent status;
- more than 1,200 veterans of the energy industry.
Volunteering
KEGOC volunteers continue to participate in various volunteer activities across the country.
The Company employees have traditionally taken part in the city’s blood donor movement and 23 September 2022 has been declared: ‘Blood Donor Day’.
761 first-graders from socially vulnerable groups in Aktobe, Atyrau, Akmola, Kyzylorda, Pavlodar, and Turkestan regions received backpacks filled with school materials and stationery as part of the ‘Road to School’ programme run by Samruk-Kazyna.
Following an appeal to the eotinish.kz portal of the Spina Bifida Society public fund, employees of the Executive Directorate, the NDC SO branch and a subsidiary raised funds for the purchase of a wheelchair. Also, a charity event was organised and held among KEGOC personnel to assist in the treatment of the son of an employee of Yuzhnye MES branch.
Employees of KEGOC and EnergoTekhProfSoyuz took part in charity events to congratulate veterans of the Great Patriotic War and home front workers on Victory Day, and provided assistance to low-income pensioners and families for the Day of Older Persons, the Kurban Ait holiday and the Power Engineer Day, and sent money to victims of the Ekibastuz Thermal Power Plant accident.
Occupational health and safety
Key Indicators
0.45
LTIFR
KEGOC held its first health and safety forum with representatives from the Ministry of Energy, Samruk-Kazyna and its PC, and companies from CIS countries.
1.08
Occupational health
and safety costs
KEGOC has received Vision Zero certification.
Management system
Key documents |
|
|
|
|
|
|
|
|
|
|
|
KEGOC Board of Directors agenda
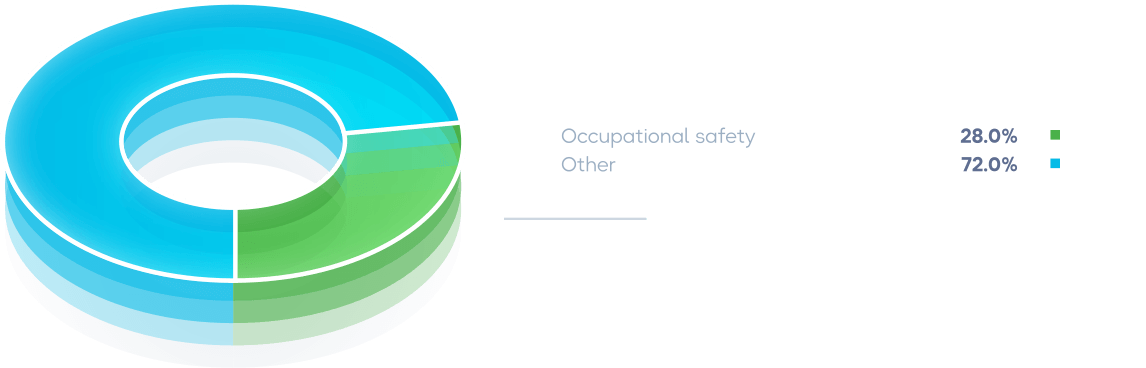
Committee on Health and Safety and the Environment agenda
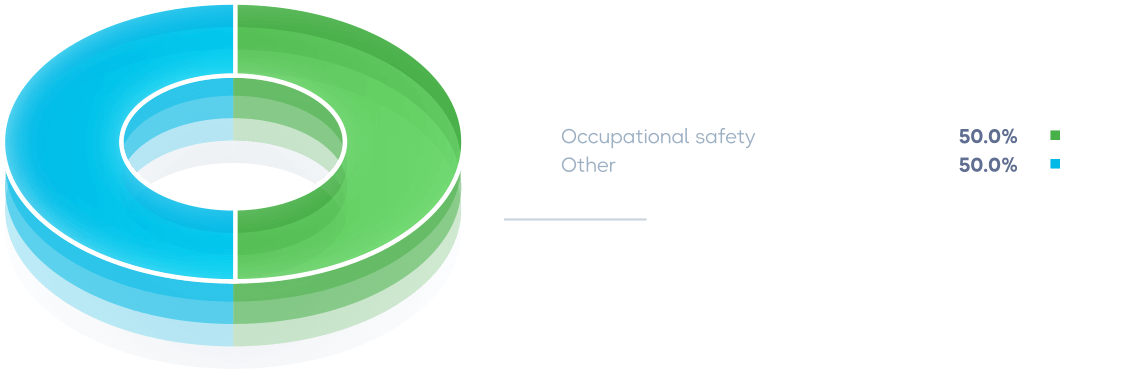
KEGOC Management Board agenda
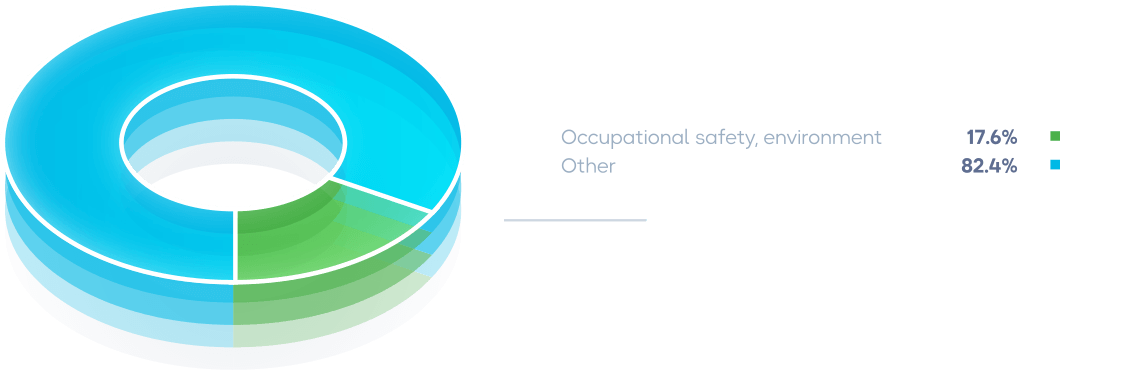
The Company’s unwavering priority are occupational safety and employee health protection. The Company is continually working to develop safe working conditions, prevent injuries during technological operations, improve operational and employee sanitary and living circumstances, and mitigate the influence of dangerous and unfavourable variables.
In October 2022, KEGOC held its first Occupational Health and Safety Forum, which was attended by representatives of the Republic of Kazakhstan Ministry of Energy, executives and HSE (Health Safety Environment) experts from Samruk-Kazyna and its member companies, KEGOC, as well as representatives from CIS companies.
During the forum, which was conducted as part of the Year of Safety and Health at Work 2022, business executives and HSE leaders discussed industrial medicine and contemporary workplace safety equipment as well as best practises for ensuring safe working conditions.
KEGOC received a certificate at the occasion from the head of the Vision Zero Kazakhstan Business Council attesting to the company’s membership in the global zero-accident movement (the Vision Zero concept, based on the three main aspects of all levels of work - safety, health and well-being, unites leading manufacturing companies all over the world).
With the aim of ensuring the effectiveness and improvement of health and safety performance and managing the pertinent risks related to the specific nature of the Company’s business, the Company has a Health and Safety Management System that covers the activities of all the Company’s business units and subsidiaries. Every year, a safety and health programme is created that outlines the required actions, associated expenses, and due dates. The Company effectively adopted the international standard ISO 45001:2018 and passed certification testing for conformity.
At least once a quarter, the operational affairs council reviews employees’ proposals for improvement of occupational safety and health conditions and outlines measures binding on the employer and employees.
Every year, workplace hazards are identified and evaluated, a risk register and a list of key health and safety risks are established, and risk mitigation strategies are developed based on the assessment results.
The risk of work-related accidents is one of the most significant risks to the Company’s operations. The following activities were carried out in 2022 to reduce this risk:
- Qualification checks on knowledge of occupational health and safety regulations;
- Analysis of video footage of operational switching operations and maintenance work;
- Safety Days;
- Unannounced inspections of workplaces in MES branches;
- Behavioural safety audits when carrying out work in the workplace;
- Monitoring of drivers’ compliance with speed limits via satellite monitoring systems and review of video recorders, and so on.
At least once every three years, the Company’s employees undergo all types of compulsory safety and labour protection training and qualification checks of their knowledge of regulations in the field of electric power industry. In 2022, additional training was conducted in accordance with the NEBOSH International General Certificate in Occupational Health and Safety standard.
Prior to admittance to work, employees are trained in safe work practices, in-service training, an initial qualification check, control drills, and workplace duplication performed under the supervision of a person responsible for training.
Mandatory pre-shift medical examinations of employees engaged in heavy work and work in harmful and/or hazardous working conditions, as well as pre- and post-shift medical examinations of drivers are carried out. Also, annual medical examinations of operational personnel are carried out to determine their health status.
No occupational diseases of the Company’s employees were reported in 2022.
KEGOC assesses the level of organisation of safe working conditions at KEGOC using the Lost Time Injury Frequency Rate (LTIFR), which includes work-related fatalities. The LTIFR is a crucial measure of a company’s health and safety performance globally. The statistic indicates the number of Lost Time Injuries (LTIs) in relation to the total number of working hours worked by the Company (Work Hours, WH), normalised to 1 million man-hours. The LTIFR for 2022 was 0.45 (compared to 0.15 in 2021).
When incidents occur, Company employees are guided by the rules governing the processes for investigating accidents, incidents and reporting on health and safety.
The causes of accidents inherent in the Company’s operations are:
- a fall from a height;
- electrical injury;
- a road traffic accident.
In 2022 there were two (2) occupational accidents involving the Company employees.
Lost time injury frequency rate
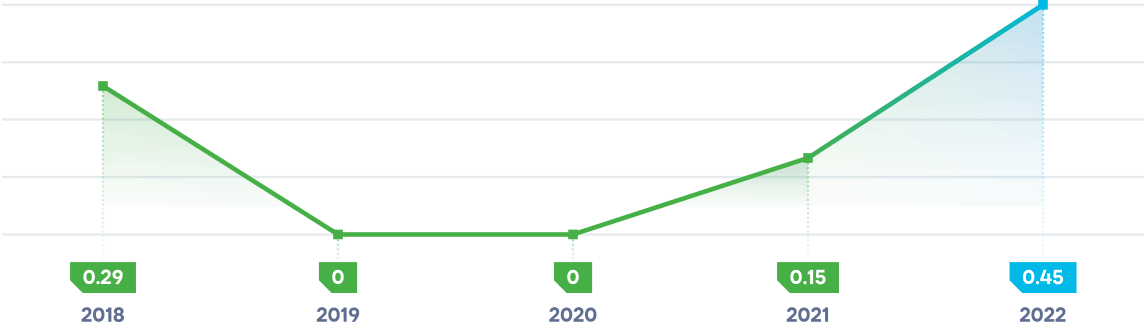